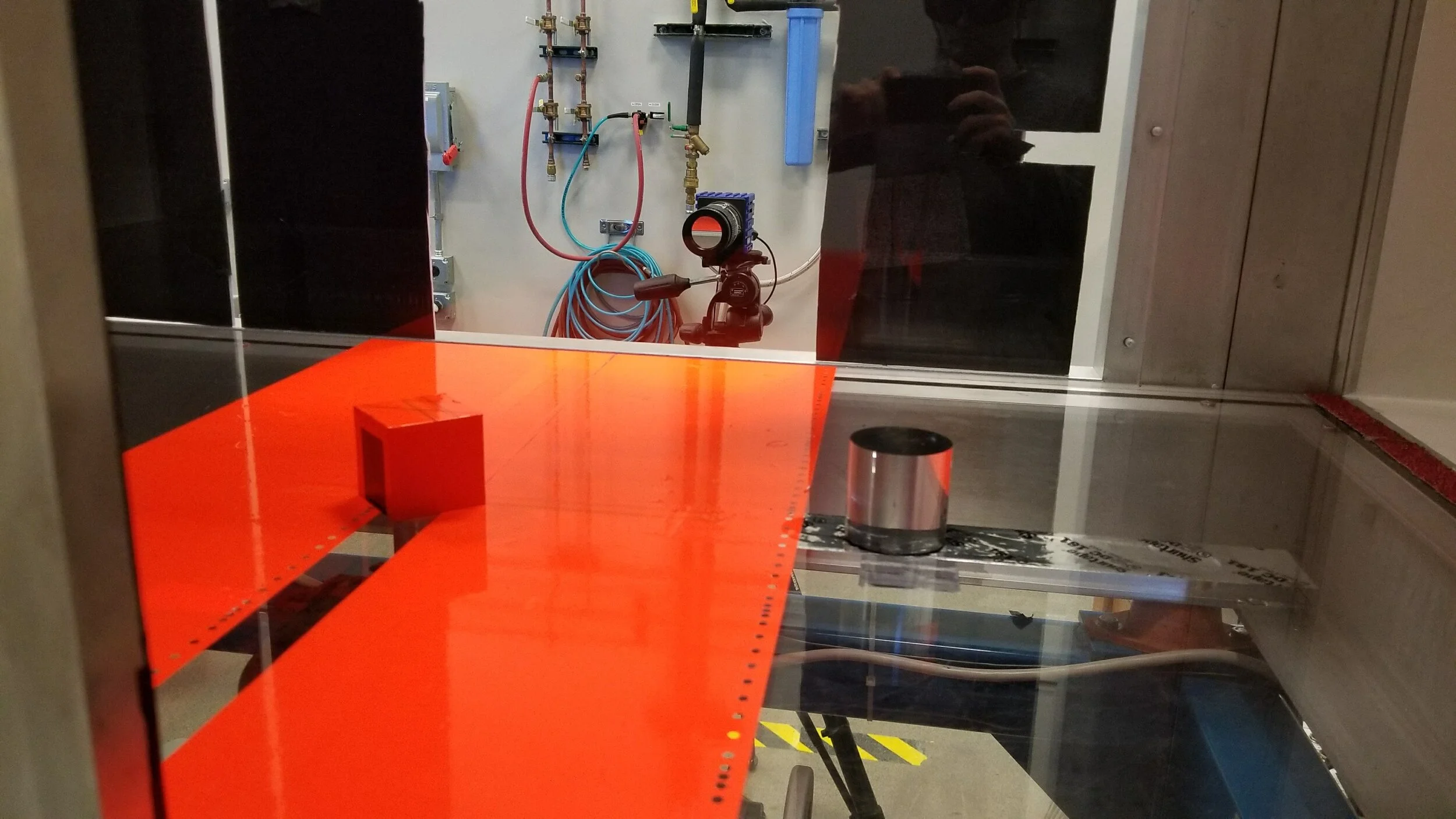
Undergraduate Research - Low-speed Wind Tunnel Testing
During undergraduate school at Florida State University, I had the opportunity to work as an undergraduate research assistant at the Florida Center for Advanced Aero-Propulsion (FCAAP). While working at FCAAP, I gained experience in the following aspects of research:
Designing, manufacturing, and setting up experiments.
Operating a low-speed wind tunnel, taking data using pressure transducers and Particle Image Velocimetry (PIV).
Post-processing and documenting experimental data.
The following images are from some of the research projects I worked on at FCAAP.
Graduate Research - Design of Automotive Structures
During graduate school at Clemson University, I had the opportunity to work as a graduate research assistant studying design of vehicle structures with the Clemson Engineering Design Applications and Research group (CEDAR). While working as a research assistant, I gained the following experiences:
Completing a Master’s Thesis on the automation of structure design for optimization.
Collaborating with design projects like Deep Orange at Clemson University’s International Center for Automotive Research (CU-ICAR).
Documentation of research projects for publication.
The following images are from an explorative tube size, shape, and orientation optimization done with Deep Orange.

Engineering Internship - Esteco North America
In fall of 2020, I had the opportunity to intern with Esteco North America as a Mechanical Engineer. In this internship, I acted as a liaison between Clemson University students and faculty, while working on a research project for the 2021 SAE WCX Digital Summit. Publication title: “Automation of a Design Optimization Process for Fiber Reinforced Polymer Sandwich Structures”
This research project focused on applying the research done through my Master’s Thesis to an experimental composite monocoque chassis for Clemson’s FSAE team. This research explored a proposed approach to optimization for a carbon fiber reinforced plastic (CFRP) and honeycomb sandwich structure.
This approach optimized the structure for each laminate’s number of plies, layup order, core sizing, material selection, orientation, and distribution laminates over the geometry. The optimizer minimized mass subject to constraints through modeFRONTIER. SolidWorks was used for the CAD parametrization and HyperWorks was used for the scripted Finte Element Analysis using Tcl/Tk.
The following images highlight steps from the above research project.